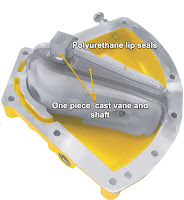 |
Click images for larger view. |
The vane actuator produces rotary motion through the application of air pressure to a "vane' attached directly to an output shaft.
There are several manufacturers of pneumatic, rotary vane valve actuators on the market. Outwardly they appear similar. Internally, there's a world of difference in their design and their performance.
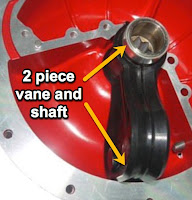
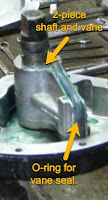
In higher quality vane actuators, the vane and shaft are machined from a single piece of steel. Casting and machining adds cost, but also adds performance. Lower quality actuators save cost by using a 2-piece vane/shaft combination. These are more likely to be affected by backlash or lost motion. In other words, a one-piece shaft and vane assembly transfers 100 percent of the vane movement directly to the shaft. Two-piece designs may lose movement over time, reducing control and accuracy.
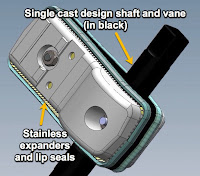
Higher quality pneumatic vane actuators incorporate a pair of “lip seals” around the vane. The durable and resilient polyurethane seals provide two key benefits; eliminating the need for o-rings; and eliminating shaft seals. Dual, opposing lip seals are located each side of the vane. They isolate the vane and shaft from the air supply and create an area from the shaft through the center of the vane that remains unpressurized, eliminating the need for pressure seals around the top and bottom of the shaft.
Some lower quality vane actuator designs use an o-ring around the entire vane, exposing the o-rings to mechanical stress and rolling. Higher quality actuators back their polyurethane lip seals with stainless steel expanders that maintain the integrity of the seal to the actuator housing.
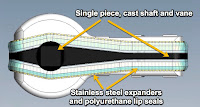
The heart of the pneumatic vane actuator is simple design. Manufacturers often promote the concept of "a single moving part", referring to the vane/shaft/seal assembly. But despite this claim, all pneumatic vane actuators are not the same. You owe it to yourself and your organization to "look under the hood". See what level of engineering and quality you're really getting.