 |
Kinetrol actuator on dense phase diverter valves |
Pneumatic conveying systems transfer powders, granules, and other dry bulk materials through an enclosed horizontal or vertical conveying line. Pressure differential and air flow is the motive force in pneumatic conveying. Through control of pressure or vacuum and the airflow inside the conveyor, the system can successfully move material.
Pneumatic conveying systems are classified into two types by their operating principle: dense phase and dilute phase.
The most common is dilute phase pressure conveying. Used for powders or granules, and most often with non-abrasive, non-fragile materials that have a light bulk density. Common examples are plastic granules, sugar, flour, corn starch, activated carbon, zinc oxide, hydrated lime, and sodium bicarbonate. Dilute phase vacuum conveying is for materials that compress under pressure, for toxic materials, and are conveyed over short distances at low capacities.
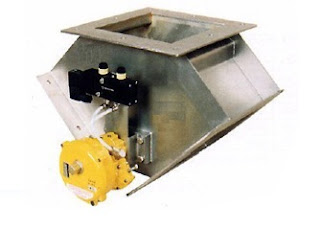 |
Kinetrol on diverter valves |
Dense phase pressure conveying is best for conveying fragile or abrasive materials over long distances. Commonly handled materials include feldspar, fly ash, silica sand, alumina, sorbitol, dextrose, carbon black, resins, cocoa beans, nuts, and certain cereals. Dense phase pressure conveying moves materials at a relatively low speed to reduce materials degradation, air consumption, and wear and tear on mechanical systems.
Diverters are used to direct the flow of conveyed material to branch lines. Because they are handling materials such as sand, gravel, whole grains, stone, cement, and coal, the diverter must be designed for handling very abrasive materials and for high cycles. Not only must the diverter be designed for this service, but the pneumatic actuator must also meet theses demanding requirements.
Kinetrol actuators have become the preferred quarter-turn pneumatic actuator for conveying diverters because of their dependability and ability to withstand tough operating environments. Kinetrol actuators are virtually immune to the high vibration, dusty atmospheres and provide years of maintenance free operation.