The Kinetrol rotary vane design is based upon a single moving part which eliminates additional parts required to convert linear motion to rotary motion. This simple and innovative design provides a highly accurate and extremely reliable actuator for operating valves, drives and dampers, and is perfectly suited for the most demanding process control applications. For more information visit www.kinetrolusa.com or call 972-447-9443.
Exploring the Superior Features of Vane Actuators in Contrast to Rack & Pinion and Scotch-Yoke Designs
Pneumatic Vane Actuators
Kinetrol Rotary Vane Actuators. Simply the Best.
Kinetrol rotary vane actuators have a well earned, and long established, reputation for performing where other pneumatic actuators fail. With outstanding cycle life, smooth and precise operation, and an environmentally rugged design, Kinetrol actuators are "simply the best" quarter-turn valve and damper actuator on the market today. Period.
For more information, contact Kinetrol USA. Call them at 972-447-9443 or visit their website at https://kinetrolusa.com.
Kinetrol Vane Actuators in Sugar Production: Suger Cane Processing

Transportation – Cane is loaded into lorries or rail trucks and taken to the mills for processing. On arrival the cane is washed to remove rocks and leaves.
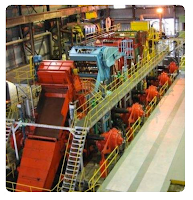
Milling – This is the extraction process whereby the sugar is removed from the cane. The shredded cane is crushed between heavy, grooved metal rollers to separate the juice from the fibre. The milling process involves a number of mills which are made up of three rollers arranged in a triangular formation. As the cane is crushed in the mills hot water (or recovered impure juice) is sprayed onto the crushed cane. The resultant dark green juice (sometimes called vesou) is then sent to a mixed juice tank for storage before clarification.
The cane fiber (called bagasse) is recycled as a fuel for the mill’s boiler furnaces. Importantly, milling must take place within 36 hours of the cane being cut.
Kinetrol units are used to control the flow of water to the spray system. It is necessary to ensure that sufficient water is used to remove the sugar content without flooding the cane.

Kinetrol units are used to control the flow of the vesou to the clarifier. Controlled flow reduces turbulence which allows for quicker settling times. Kinetrol's are also be used to control the recirculation flow of the sugar juice to the clarifier.
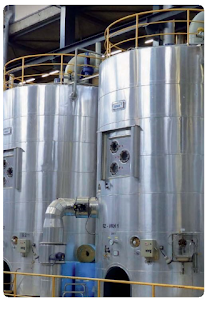
Kinetrol actuators are used to control the flow of steam to the evaporation tanks. In addition they control the flow of the juice through the evaporators. This is because of their reliability in the higher ambient temperatures in the process area.
Vacuum Pans – The syrup is concentrated further by boiling it in vacuum pans. Here it is ‘seeded’ with small sugar crystals to allow crystallization to take place. When the the sucrose concentration reaches the desired level the mixture of crystals and syrup, called massecuite, is sent to the centrifuges.
Kinetrol actuators control the input of heating steam into the pans as well as the flow of the massecuite through the process.
Centrifuges – High speed centrifuges separate the massecuite into sugar crystals and by-products (molasses).
Kinetrol actuators control the massecuite feeding system into the centrifuges. Accurate control of the valves feeding the centrifuges is necessary to prevent overloading and leakage of the centrifuges.
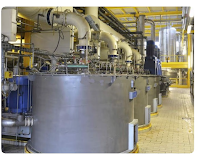
Dryers – Damp sugar crystals are dried in heated dryers before being sorted in sizes and either packed or stored.
Kinetrol's reliability, especially under hot, humid conditions, are crucial factors for our units being used within the sugar industry. Depending on the plant and location the actual ‘processing’ season varies from around four months for sugar beet to six months for sugar cane. During this short time it is essential that plants have no production issues as this will have a dramatic effect on the productivity and therefore competitiveness of the plant. The reliability and robustness of the Kinetrol units means they continue to function through each production season year after year.
Kinetrol’s ability to maintain an unchanged torque rating even with wear of the lip seals, means critical valves continue to function correctly over time. This is especially true with a product that is highly viscous in the later stage of production (e.g. thick juice, molasses).
With some plants being non-operational for many months of the year there does exist time for service & maintenance or replacement of rack & pinion actuators. However as margins within the sugar industry are low, the total cost of ownership for Kinetrol units over a number of production seasons makes them a more cost effective solution.
For more information, contact Kinetrol USA by calling 972-447-9443 or by visiting https://kinetrolusa.com.
Kinetrol Vane Actuators
Kinetrol is the inventor of the quarter turn pneumatic vane actuator and manufactures 16 sizes with torque outputs ranging from 8 lb inches to 168,000 lb inches when supplied with 100 psig.
Kinetrol’s exclusive direct-mount modular concept eliminates expensive and unnecessary tubing, fittings, brackets and couplings, which provides virtually hysteresis-free and extremely compact, automated assemblies. Unlike cylinder actuators, Kinetrol’s one piece vane and shaft design move as one resulting in extremely precise modulating and on/off control. Kinetrol actuators use double opposed polyurethane lip seals instead of O-ring seals typically used in quarter turn actuators. Kinetrol’s lip seal design isolates the shaft seal from plant air pressure and also acts as wiper for any foreign material which dramatically extends the service life of these actuators in all applications.
Knock off and copy attempts have come and gone over Kinetrol’s 60 plus year history, but none have come close to Kinetrol’s stellar track record of quality and reliability. Truth is in the performance and Kinetrol actuators have developed the reputation as the most reliable severe service, high cycle actuators the world over since 1958.
Proven Dependability: Kinetrol Vane Actuators
Kinetrol USA
https://kinetrolusa.com
972-447-9443
Demonstration of NAMUR Mount Solenoid Valve with Manual Bypass Option on Kinetrol Actuator
Kinetrol Actuators Protect People and Property with Reliable Performance in Chemical Plant Fire
![]() |
The Kinetrol actuator is completely unrecognizable, having been melted in a fire. |
The building houses a $30 million dollar compressor that supplies process air to reactors to begin the PTA manufacturing process.
As part of the safety system, (2) two 6" class 150 high performance butterfly valves with Kinetrol 097-120 and open/closed limit switches were installed on process air lines of one production unit.
During the fire, the two Kinetrol actuated valve assemblies performed exactly as required, shutting the valves tightly and keeping them shut even after the heat of the fire completely melted the actuator housings.
![]() |
Closer view. |
For more information, contact Kinetrol USA by calling 972-447-9443 or by visiting https://kinetrolusa.com.
A Review: Why Kinetrol Actuators Are the Most Reliable 1/4 Turn Pneumatic Actuator on the Market Today
![]() |
Click on image for larger view. |
- Durable epoxy stove enamel exterior finish.
- Long life epoxy or PTFE internal finish.
- Integral vane/shaft casting - only one moving part: Simplest and most reliable mechanism for quarter-turn rotary actuation.
- Manual override square and position indicator.
- Stainless steel expanders ensure long term lipseal / case contact.
- Double opposed, Polyurethane, lip seals for effective sealing and long maintenance free life.
- Space filling/energy absorbent sideplates (polymer or metal).
- Corrosion resistant zinc (non-incendive) or aluminum alloy case.
- Easy stop adjustment at each end of stroke for accurate seating.
- Close couple control modules. Fail-safe spring returns, limit switches, positioners and solenoid valves all close couple to the actuators.
- No cranks or gearing. No power loss or backlash - allows accurate positioning.
- Long maintenance-free life. Up to 4 million operations guaranteed.
- Compact - space saving - efficient. Best torque/size package available, fast operating speeds, best air consumption, proven design.
- Unique serial number for identification and traceability.
Kinetrol Vane Actuators: Performance Under Pressure
Words Used to Describe Kinetrol Actuators
The Most Reliable 1/4 Turn Pneumatic Actuator on the Market Today. Period.
For over 50 years Kinetrol has been providing trouble-free valve and damper actuators to the chemical, biofuel, food & beverage, metal, mineral, oil, gas, pharmaceutical, power generation, paper, textile, water, wastewater, and transportation industries.https://kinetrolusa.com
972-447-9443
Pneumatic Valve Actuator Assembly Designed to Prevent Water Hammer
![]() |
Kinetrol vane actuator and dashpot assembly |
The "hammering" is due to a pressure wave created by the instantaneous change in fluid velocity when a valve is suddenly closed or opened. Controlling valve closure time is one of the most economical ways to minimize water hammer. To do this efficiently, while still meeting the process requirements, the use of a variable speed mechanism to control valve stroke is used. One unique, economical and space savings approach is to use a pneumatic vane actuator coupled with a rotary damper (or dashpot).
Rotary dashpots are precision fluid damping devices which give a smooth resistance to shaft rotation which increases with angular velocity.
In this case, a pump station in the USA was having repeated problems with a large, open reservoir hydraulic actuator used to dampen valve opening and closing. It was overly cumbersome and costly to maintain.

The addition of the bi-directional, sealed dashpots smooth the normal travel, damp any valve flow induced disc oscillations, and provide at least 40 seconds travel time on air and/or electrical power failure.
Using pulsed outputs with programmable delay between steps, the actuators provide a 10 minute opening & closing time for the full 90 degree travel. The system is adjustable between 3-15 minutes with less than one degree increments., and other opening and closing ranges are available. The actuators use fail-free logic, but fail-hold & fail-safe are available.
These assemblies were commissioned in early Fall of 2017 and are working very well. Their use will be replicated at other pump stations operated by the same customer.
![]() |
This open reservoir hydraulic actuator was huge and a maintenance headache. |
Integral Vane-Shaft Actuators Best for High Cycle Rate and Modulating Applications
![]() |
Internal view of vane actuator. Note the single piece vane/shaft design. |
Why? Because of the mechanical problems inherent to the use of gears.
According to Wikipedia, "A gear or cogwheel is a rotating machine part having cut teeth, or cogs, which mesh with another toothed part to transmit torque."
- Friction
- Fretting Wear
- Backlash
"Fretting wear" is caused by the repeated cyclical rubbing between two surfaces (gears in the case of scotch yoke or rack and pinion actuators) and over a period of time, will remove material from one or both surfaces.
Backlash happens when gears change direction. It is caused by the gap between the trailing face of the driving tooth and the leading face of the tooth behind it. The gap must be closed before force can be transferred in the new direction, hence the phenomena of backlash. This is also sometimes referred to as "slop".
For any questions about applying the most appropriate type of actuator for any valve or damper application, call Kinetrol at 972-447-9443 or visit http://www.kinetrolusa.com.
Kinetrol Product Line Video
For over 50 years Kinetrol has been providing trouble-free valve and damper actuators to the chemical, biofuel, food & beverage, metal, mineral, oil, gas, pharmaceutical, power generation, paper, textile, water, wastewater, and transportation industries.
The Toughest Pneumatic Actuators on Earth
The Kinetrol vane actuators' outstanding cycle life, smooth and precise movement, and environmentally rugged design makes it the best choice for all of your valve actuation and damper drive requirements.
For more information visit http://www.kinetrolusa.com or call 972-447-9443.
Review: Vane Actuators
![]() |
An internal view of a vane actuator allowing you to see the one piece vane and shaft, lip seals, travel stops, and the clam shell design. |
The vane includes “lip seals” that isolate the vane and shaft from the air supply. The lip seal design provides several advantages, namely eliminating the need for shaft seals and an inherent cleaning action internally. A split, or “clam-shell” housing is assembled around the vane, totally enclosing it. When supply air is applied to one side of the vane, torque is produced moving the vane in one direction. Accordingly, there is direct rotary motion transfer to the shaft, with 100% efficiency. Torque is controlled by surface area of the vane and the differential pressure on either side of the vane. Bi-directional over-travel is limited by the use of travel stops mounted in both sides of the housing.
![]() |
The Kinetrol Vane Actuator |
For more information about vane actuators visit http://www.kinetrolusa.com or call 972-447-9443.
Why Vane Actuators Outlast and Outperform Rack & Pinion and Scotch Yoke Designs
![]() |
Kinetrol vane actuators perform in the toughest applications. |
Kinetrol's design is based upon a single moving part, which eliminates additional parts required to convert linear motion to rotary motion. This simple and innovative design provides a highly accurate and extremely reliable actuator for operating valves, drives and dampers, and is perfectly suited for the most demanding process control control applications.
For more information, visit http://www.kinetrolusa.com
Valve Actuators for Bottom Ash High Pressure Spray Removal
![]() |
Coal burning power plant |
![]() |
Kinetrol Rotary Vane Actuator |
Its crucial that the double offset valves seat completely and are truly “zero-leakage”. In this high pressure and high abrasion scenario, even the slightest leak will cause a rapid failure of the valve seat.
Rack and pinion, scotch yoke, and electric actuators are problematic because of the inherent hysteresis in their gearing. This hysteresis compounds over time adding to the amount of error introduced and increasing the likelihood of a poorly closed valve.
Rotary vane actuators, on the other hand, provide “hysteresis-free” seating due to their single moving part and one piece vane and shaft design. When mounted to the butterfly valves with a no-play coupler, the valve disc is guaranteed to close tightly, without degradation over time.
Additional benefits of using the vane actuator is smooth, controlled closing to reduce the possibility of water hammer and the greater ability work in poor quality atmospheres, both of which are considerations for this application.
What Is a Vane Actuator?
![]() |
Inside view of a vane actuator showing the clam-shell design, internal chamber layout, and double-sided vane. |
Linear motion gas/hydraulic cylinder or piston actuators use gears to convert linear to rotary motion. Vane actuators employ a rigid vane inside a sealed chamber that is connected directly to the drive shaft at one end with no gears. The result is much smoother rotary movement and greater cycle life.
Vane actuators operate by introducing a fluid or gas to either side of it's enclosure through inlet/outlet ports, creating the force required for movement. Advanced vane actuators utilize double sided vanes that allow for pressurization of both sides, allowing for bi-directional movement. The vane itself provides an arc movement in the far side (opposite the shaft) of the actuator, translating rotary movement back to its integrated shaft.
The vane actuator shaft is designed to connect directly to a device (valve, damper, ergo mechanism) for the transfer of movement. In advanced design vane actuators, the shaft is completely sealed from the pressurized side of the vane via “lip seals” which act to prevent the loss of air/gas/oil through shaft seals or bearings. With the help of spring steel supports, the lip seals are kept in constant contact with the inner surface of the chamber wall at all times during rotation. A side benefit of lip seals are the self-cleaning or sweeping action they provide to the inside chamber surfaces.
Since the double-sealed vane separates the vane actuator chamber in two sides, movement in either direction can be changed merely by creating a pressure differential on either side of the vane. Inlet/outlet ports allow for the pressurization and de-pressurization for either side. As gas or fluid is introduced to one side, the vane is forced away, toward the opposite side. By reversing the pressure and vent ports, and pressurizing the opposite chamber, the actuator moves in the opposite direction.
When vane actuators use only gas or fluid as their source for movement in both directions, they are referred to as “double acting”. When an optional spring is used to provide the power in one direction (open or close) they are referred to as “spring return”.
For more information on vane actuators, visit http://www.kinetrolusa.com
Hear Kinetrol USA's Neil Meredith Interviewed at WEFTEC 2016
![]() |
Neil Meredith |
WEFTEC®, the Water Environment Federation’s Annual Technical Exhibition and Conference, is the biggest meeting of its kind in North America and offers thousands of water quality professionals from around the world the best water quality education and training available today. Also recognized as the world’s largest annual water quality exhibition, WEFTEC’s massive show floor provides unparalleled access to the field’s most cutting-edge technologies and services.
Kinetrol actuators are widely used in municipal water systems across the United States and are known for their outstanding performance, durability, and extreme high cycle life.