![]() |
Kinetrol's AP pneumatic positioner. |
The result is a positioner with unparalleled performance and real industrial robustness, easy to calibrate and characterize, and adaptable to the whole range of applications with a great list of options:
- High flow valves
- Direct mount or industry standard discrete mount housings
- 4-20mA angle retransmit
- Limit switches
- Clear Cone position monitor
- I/P convertors (either simple or with various explosion proof options)
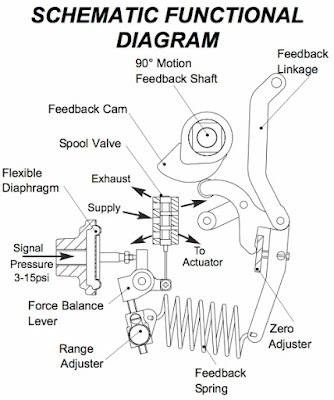
The AP positioner is designed to drive a rotary or linear actuator to a position set by a 3-15 psi (0.2-1.0 bar) signal and hold it there until the signal changes.
When a signal pressure is applied to the diaphragm it moves the force balance lever clockwise against the tension of the feedback spring. This moves the spool valve, supplying air pressure to one side of the actuator while exhausting trapped air from the other side. The feedback shaft follows the movement of the actuator and turns the cam counter clockwise, pushing the cam follower and increasing the tension on the feedback spring until it balances the force on the diaphragm and moves the spool valve to its central ‘hold’ position.
The relationship between the input signal and desired position (the ‘characteristic’) is determined by the cam profile. A linear 3-15 psi (0.2 - 1.0 bar) signal / 0-90° output movement cam is standard. Split range, fast opening, equal percentage or customized characteristic cams are available.
See the brochure below for detailed information and illustrations. For more information, contact Kinetrol USA at http://www.kinetrolusa.com or call 972-447-9443.