The Kinetrol rotary vane design is based upon a single moving part which eliminates additional parts required to convert linear motion to rotary motion. This simple and innovative design provides a highly accurate and extremely reliable actuator for operating valves, drives and dampers, and is perfectly suited for the most demanding process control applications. For more information visit www.kinetrolusa.com or call 972-447-9443.
Happy New Year from Kinetrol USA!
All of us at Kinetrol USA wish our customers, distributors, colleagues and friends a very happy and prosperous 2018!
Kinetrol Blueline Pneumatic Actuator - Features
Features of the Kinetrol Blueline pneumatic actuator:
- Durable Blueline coating meets FDA and BfR L1 specifications.
- Corrosion resistant zinc (non-incendive) or aluminum alloy case.
- Easy stop adjustment at each end of stroke for accurate seating.
- Long life epoxy or PTFE internal finish.
- Integral vane/shaft casting - only one moving part.
- Manual override square and position indicator.
- Space filling/energy absorbent sideplates (polymer or metal).
- Double opposed, Polyurethane, lip seals for effective sealing and long maintenance free life.
- Stainless steel expanders ensure long term lipseal / case contact
Kinetrol Actuator Feature Video
Here's a new Kinetrol vane actuator feature video. Please take a minute to watch. Hope you enjoy.
Pneumatic Actuators Well-suited for Offshore Valve and Damper Applications
![]() |
Offshore Platform |
Corrosion
![]() |
Corrosion resistant housing and sealed spring. |
Vibration
Constant structural vibration, caused by the dynamic forces generated by compressors, pumps, and engines, leads to poor equipment reliability and eventual failure. Pulsating and shaking forces expedite wear on mechanical connections such as gears and yoke mechanisms, with many gear failures due to resonant vibration.
Space
Oil platform actuators, control valves, safety valves, and piping systems are configured very similarly to their terra firma cousins, with the major difference between land and platform equipment being reduced weight and size. Space is at a premium and it is critical to keep equipment as compact as possible.
![]() |
Single moving part. No gears or yokes. |
Kinetrol rotary vane actuators provide an excellent solution, well-suited for off-shore and marine applications. A durable epoxy stove enamel finish and corrosion resistant zinc (non-incendive) or aluminum alloy case protect the actuator from the harsh environment.
![]() |
Size comparison for similar output. |
Finally, Kinetrol vance actuators only require 1/3 to 1/2 the required installation space of similarly equipped rack and pion actuators.
For more information, contact Kinetrol USA by visiting https://www.kinetrolusa.com or calling 972-447-9443.
Vane, Shaft and Seal Design: The Critical Difference in Pneumatic Rotary Valve Actuators
![]() |
Click images for larger view. |
There are several manufacturers of pneumatic, rotary vane valve actuators on the market. Outwardly they appear similar. Internally, there's a world of difference in their design and their performance.
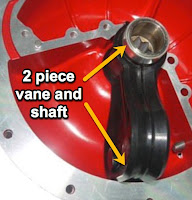
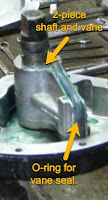
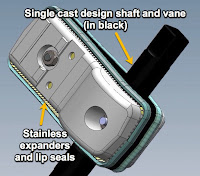
Some lower quality vane actuator designs use an o-ring around the entire vane, exposing the o-rings to mechanical stress and rolling. Higher quality actuators back their polyurethane lip seals with stainless steel expanders that maintain the integrity of the seal to the actuator housing.
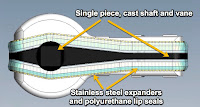
How Kinetrol Pneumatic Rotary Vane Actuators Work
Kinetrol pneumatic rotary vane actuators use a one piece vane and shaft produce rotary torque on the shaft output drive. The vane is assembled inside a 2-piece clam-shell enclosure. The presence of the vane creates two air chambers. By pressurizing and venting opposing chambers, the resulting pressure differential across the vane provides torque to the shaft. Torque output of the rotary vane actuator remains constant throughout the full rotation of the shaft.
http://www.kinetrolusa.com | 972-447-9443
http://www.kinetrolusa.com | 972-447-9443
Kinetrol Pneumatic Actuators for Portland Cement Production
![]() |
Cement valve using Kinetrol Actuator |
Typically, these raw materials are obtained from open-face quarries, underground mines, or dredging operations. When mining, pockets of pyrite, which significantly increase emissions of sulfur dioxide (SO2), can be found in deposits of limestone, clays, and shales used as raw materials for portland cement.
Transport of the raw materials is accomplished by a variety of mechanisms, including screw
conveyors, belt conveyors, drag conveyors, bucket elevators, air slide conveyors, and pneumatic conveying systems. A variety of valves, gates, and dampers are required to accurately control the flow of raw materials as they are being discharged from pipes, silos, bins and hoppers. These flow control devices all have one thing in common - the actuators that control their opening and closing are exposed to extremely dusty and dirty atmospheres, with significant amounts of vibration - and they are almost always located in an area where repairs are very costly.
Kinetrol vane actuators are used to automate these gate, butterfly and mixer valves because of their ruggedness and their reliability. Additionally, Kinetrol pneumatic actuators have a smaller footprint and consume less air compared to other pneumatic actuators or conventional linear pneumatic cylinders, resulting in significant savings in energy costs.
Subscribe to:
Posts (Atom)