 |
Coal burning power plant |
The pulverized coal boiler is the most common type of coal-burning furnace in the electric utility industry. After the pulverized coal is burned in a dry, bottom boiler, approximately 80 % of the unburned material or ash gets captured and recovered as fly ash. The remaining 20% of ash is categorized as bottom ash, a dark gray, granular, porous ash that is collected in a water-filled hopper at the bottom of the furnace. When a sufficient amount of bottom ash is collected in the hopper, it is
purged by high pressure water jets into sluiceways or other conveyances for further processing.
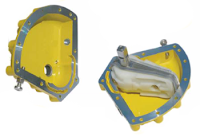 |
Kinetrol Rotary Vane Actuator |
The high pressure water (approx. 400 PSI) is actually recycled ash water and is very abrasive. The valves and control systems used to move the bottom ash slurry are typically 3” to 12” double offset, high-performance butterfly valves. Double acting pneumatic actuators are most common for opening and closing. Cycle frequency varies, but most typically are between 3 to 12 times per day.
Its crucial that the double offset valves seat completely and are truly “zero-leakage”. In this high pressure and high abrasion scenario, even the slightest leak will cause a rapid failure of the valve seat.
Rack and pinion, scotch yoke, and electric actuators are problematic because of the inherent hysteresis in their gearing. This hysteresis compounds over time adding to the amount of error introduced and increasing the likelihood of a poorly closed valve.
Rotary vane actuators, on the other hand, provide “hysteresis-free” seating due to their single moving part and one piece vane and shaft design. When mounted to the butterfly valves with a no-play coupler, the valve disc is guaranteed to close tightly, without degradation over time.
Additional benefits of using the vane actuator is smooth, controlled closing to reduce the possibility of water hammer and the greater ability work in poor quality atmospheres, both of which are considerations for this application.